Verschleißschutz durch metallische Pulver
Im Forschungsprojekt „WearECO-Enamel“ entwickelt ein Team im Labor Werkstofftechnik auf dem Technologie-Campus Steinfurt eine pulvermetallurgische Verschleißschutzbeschichtung weiter. Hierzu soll eine neuartige Emaille entwickelt werden.
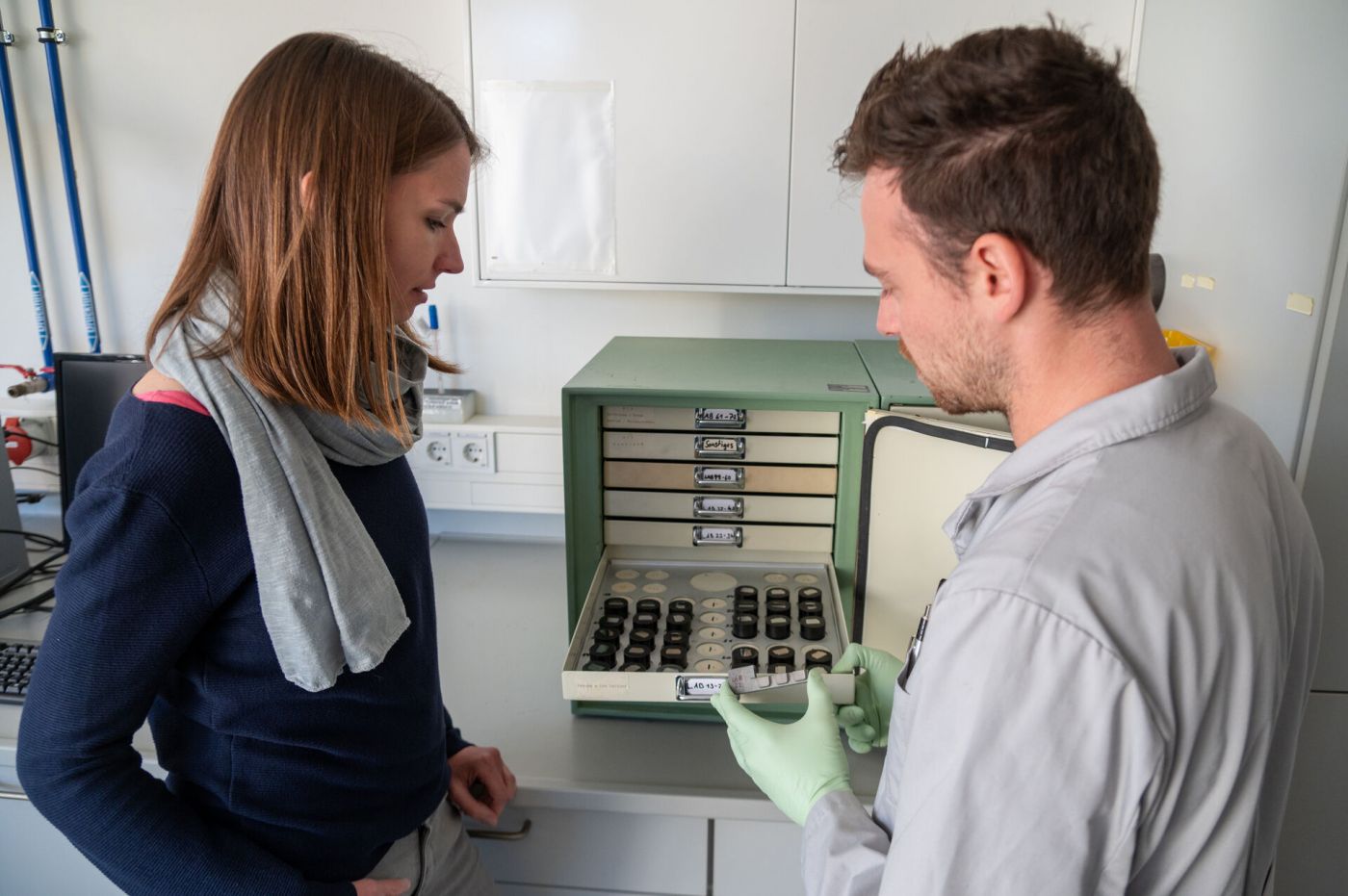
Im Forschungsprojekt "WearECO-Enamel" untersucht das Team Verschleißschutzschichten. Prof. Dr. Miriam Laubrock und Jan Philipp Berges wählen die passende Probe aus. (Foto: FH Münster/Frederik Tebbe)

Jan-Philipp Berges bereitet die Probe zur Untersuchung vor… (Foto: FH Münster/Frederik Tebbe)
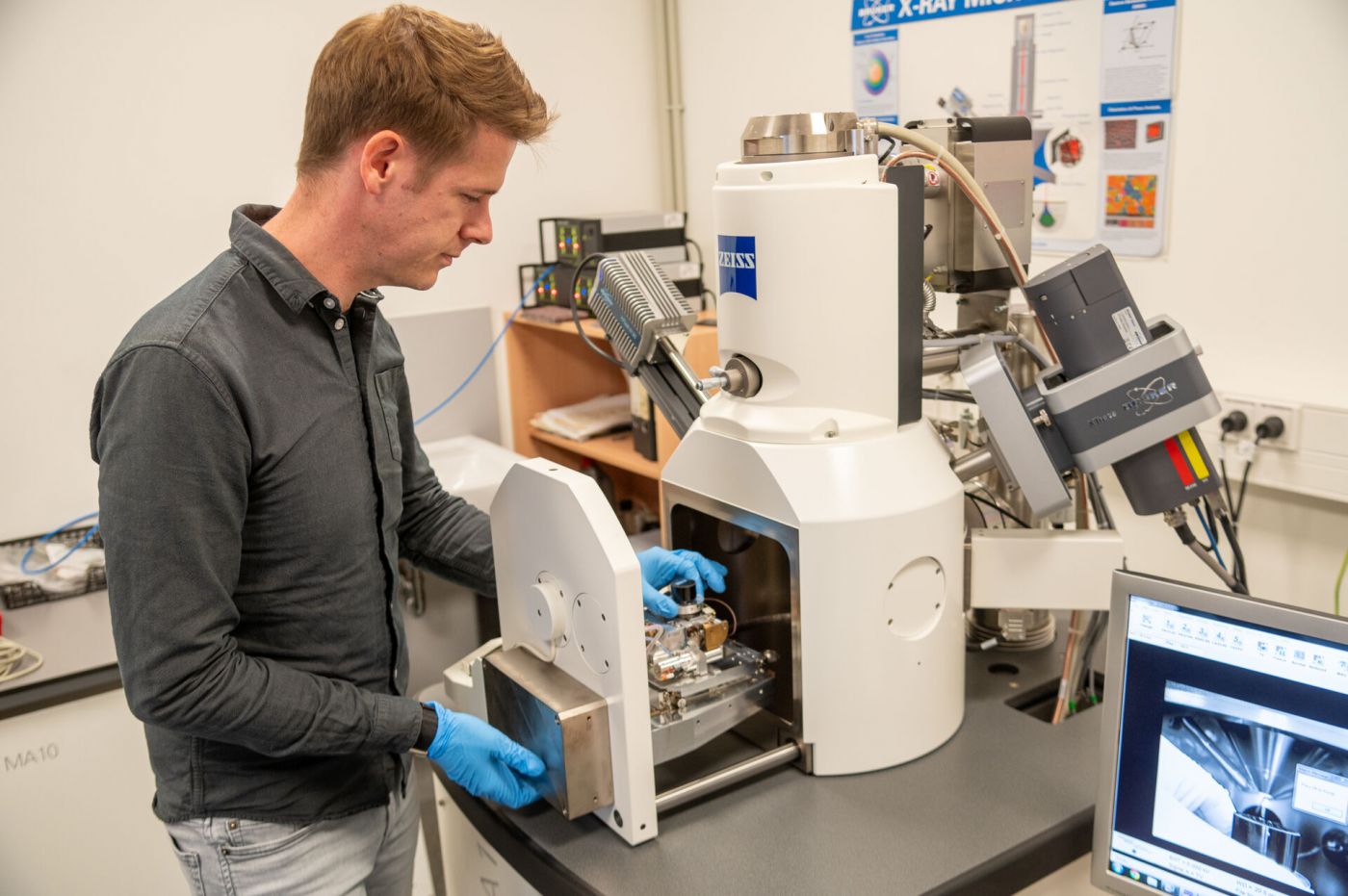
…und Dr. Tobias Schniedermann untersucht sie anschließend im Rasterelektronenmikroskop. (Foto: FH Münster/Frederik Tebbe)
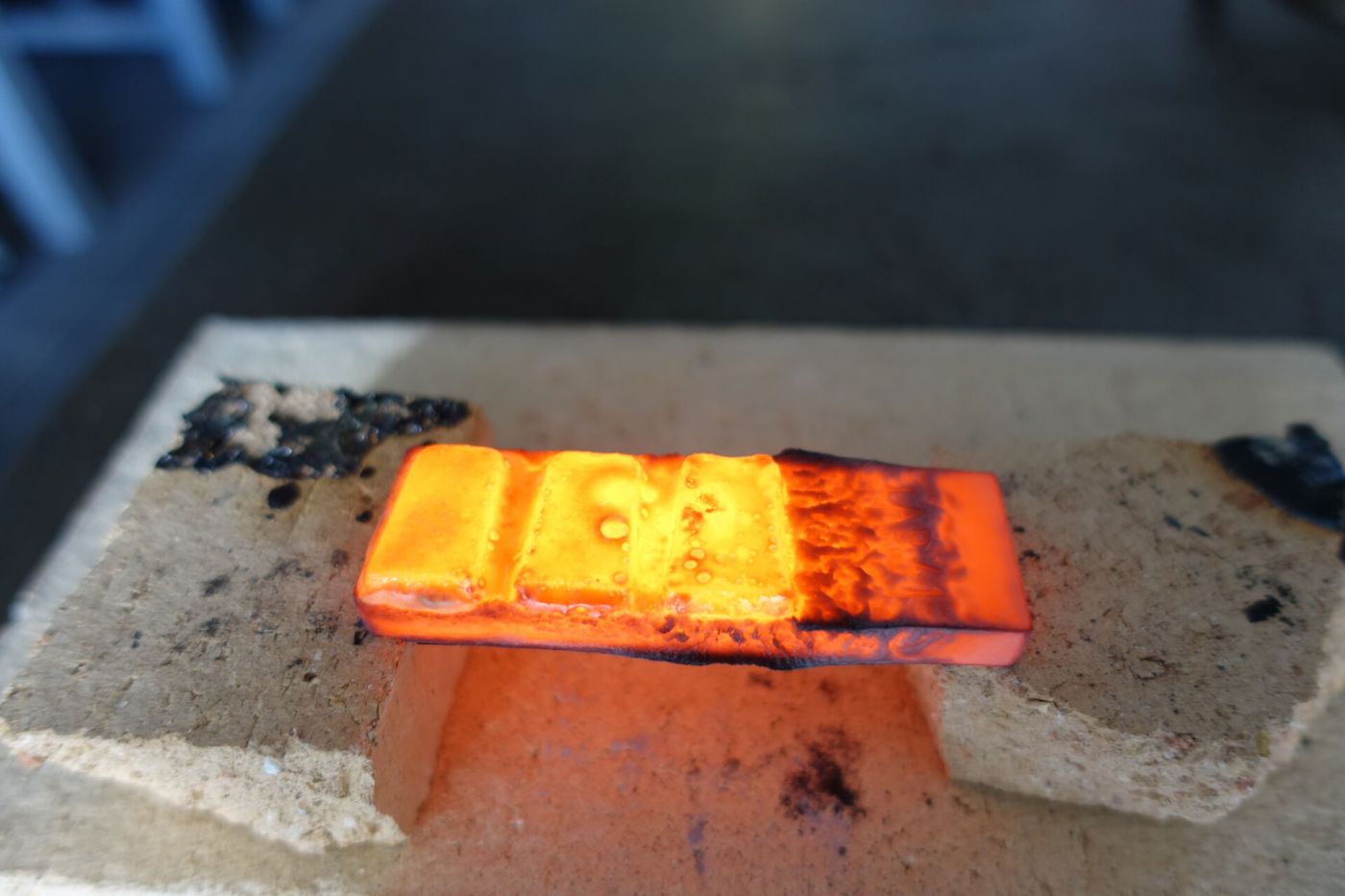
Bei über 1.000 Grad Celsius verschmelzen feine Metallpartikel zu einer widerstandsfähigen Schutzschicht auf Bauteilen. Die für den Einschmelzprozess benötigte Emaille will das Team optimieren. (Foto: FH Münster/FB Maschinenbau)
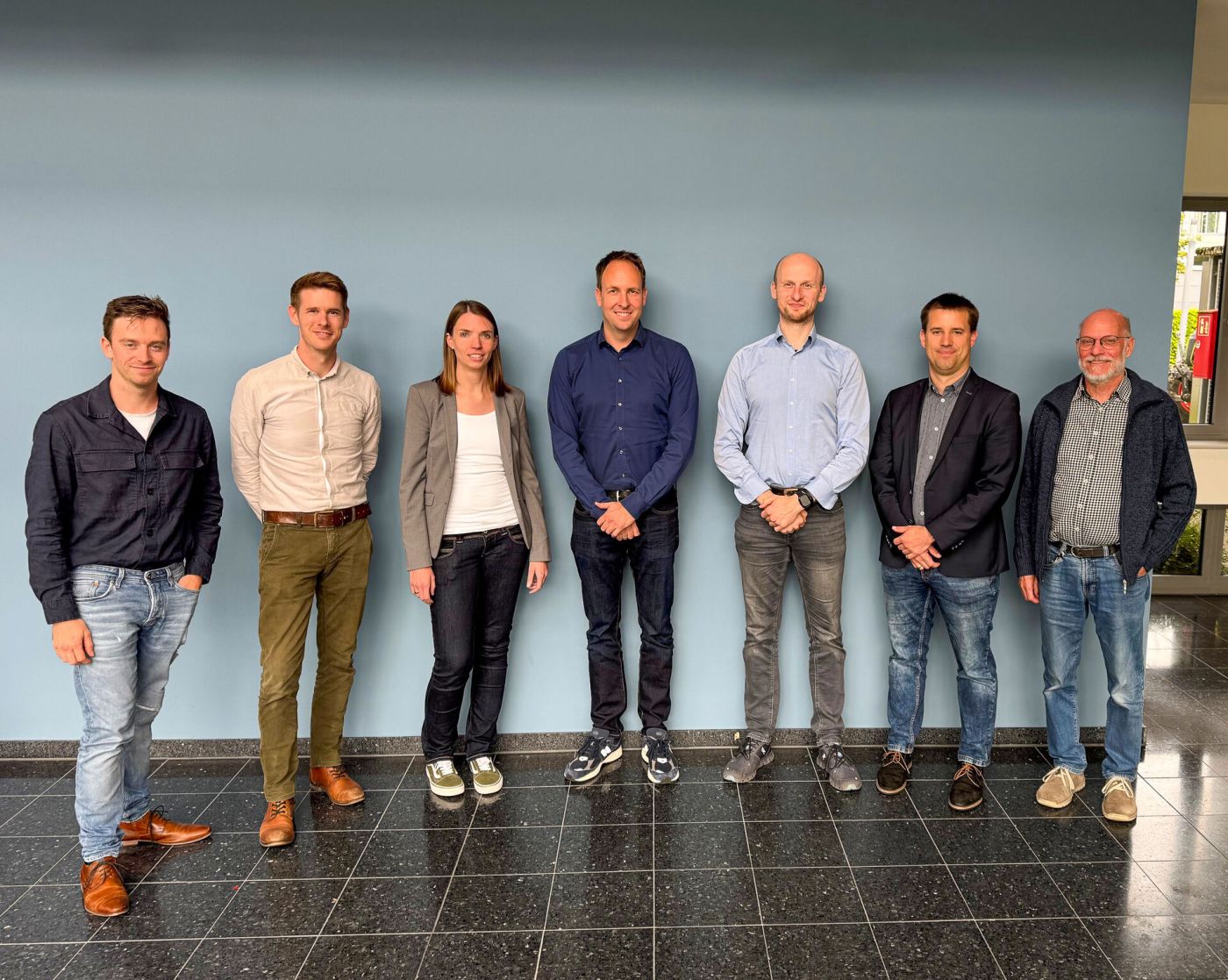
Das Projektteam (v.l.): Jan Philipp Berges, Dr. Tobias Schniedermann, Prof. Dr. Miriam Laubrock (alle FH Münster), André Petzak (Jäckering), Marcel Rettler (Jäckering), Benedikt Kegel (Wendel), Prof. Dr. Jürgen Peterseim (FH Münster). (Foto: FH Münster/FB Maschinenbau)
Eine Beschichtungstechnologie weiterentwickeln, die die Verschleißbeständigkeit von Maschinen und Anlagenbauteilen erhöht – das war das Ziel des nun erfolgreich abgeschlossenen Forschungsprojekts „Ultra-Coat“ am Fachbereich Maschinenbau unserer Hochschule. Ein Team um Prof. Dr. Jürgen Peterseim und Dr. Tobias Schniedermann hat die Pulverpartikel, die als Paste auf ein Bauteil aufgetragen und bei über 1.000 Grad Celsius im Kammerofen verschmolzen werden, auf eine konkrete Problemstellung in der Industrie angewandt und Mühlenbauteile der Altenburger Maschinen Jäckering GmbH damit beschichtet. „Doch wenn man in der Forschung eine Frage beantwortet hat, tun sich zehn neue auf“, sagt Schniedermann. Deshalb untersucht er gemeinsam mit der neuberufenen Professorin Dr. Miriam Laubrock und dem wissenschaftlichen Mitarbeiter Jan Philipp Berges im Labor Werkstofftechnik, Fügetechnik, Oberflächentechnik die von unserer Hochschule patentierte Technologie im Folgeprojekt „WearECO-Enamel“ weiter: Die Emaille, die beim Einschmelzprozess als Oxidationsschutzschicht über der eigentlichen metallischen Schutzschicht aufgetragen wird, ist noch nicht so ausgereift, dass das Verfahren wirtschaftlich tragbar ist. Das soll das von der Deutschen Bundesstiftung Umwelt (DBU) geförderte Projekt ändern und sie damit zur Marktreife führen.
„Derzeit müssen wir drei Schichten unterschiedlicher Emaille auftragen“, erklärt Berges. „Aber unser Ziel ist es, eine neue Emaille zu entwickeln, von der wir nur noch eine Schicht benötigen, um Kosten einzusparen und trotzdem das gleiche Ergebnis zu erzielen.“ Dazu arbeitet das Team mit der Wendel GmbH aus dem hessischen Dillenburg zusammen, die Emaille herstellt: „Die Firma entwickelt verschiedene Probezusammensetzungen, aus der sämtliche Stoffe entfernt werden, die nicht für unser Verfahren nötig sind“, so Laubrock. „Dazu gehören etwa farbgebende Stoffe oder Haftmittel. Die Emaille – man kennt sie zum Beispiel von Badewannen, Kochtöpfen oder Straßenschildern – muss bei uns weder lange halten noch dekorativ sein, sondern nur ihre Funktion als Oxidationsschutzschicht während des Beschichtungsvorgangs erfüllen.“ Wendel bringt hierbei ebenfalls die nötige Expertise im Bereich der Auftragsverfahren mit, sodass die neuartigen Emaillen möglichst wirtschaftlich und ressourceneffizient aufgebracht werden können.
Dem Projekt liegt die 2021 von Peterseim und Schniedermann erfundene „Haduflex“-Technologie zugrunde, die seitdem kontinuierlich weiterentwickelt wird. „Verschleißschutz ist Umweltschutz“, erklärt Schniedermann die Dringlichkeit des Forschungsvorhabens. „Die Technologie kann dazu beitragen, Ressourcen in Industrieprozessen deutlich zu schonen.“ Den Luftwirbelmühlen der Jäckering GmbH konnte das Team im Vorgängerprojekt bereits maßgeschneiderte Lösungen bieten, um Materialien bei geringerem Abrieb zu zerkleinern. „Sobald wir die passende Emaille entwickelt haben, wollen wir unsere Beschichtungen erneut bei der Firma Jäckering, die ebenfalls Projektpartner ist, testen“, so Schniedermann.
„WearECO-Enamel“ wird von der DBU mit rund 237.000 Euro gefördert. Das Projekt läuft für 18 Monate.