Was ist eine Supply Chain?
Wie werden Supply Chains organisiert?
Die große Herausforderung besteht darin, die auf verschiedene Unternehmen verteilte Wertschöpfung zusammen mit den Logistiksystemen zu koordinieren, und zwar zum Vorteil aller beteiligten Partner. Damit umfasst das "Supply Chain Management" die partnerschaftliche Planung, Steuerung und Weiterentwicklung von Lieferketten mit dem Ziel der Optimierung betrieblicher Ergebnisse sowie der Liquidität unter Beachtung sozialer und ökologischer Ziele.
Da sich die häufig vielen Unternehmen einer Supply Chain beim Management eng abstimmen müssen, kommt es oft zu der Schwierigkeit, alle Ziele und Interessen aufeinander abzustimmen. Dies wurde in den 90er-Jahren erkannt. Es konstituierte sich das Supply Chain Council (SCC), welches ein Standardmodell zur Beschreibung, Analyse und Gestaltung von Lieferketten entwickelte, das so genannte "Supply Chain Operation Reference (SCOR)"-Modell. Betrachtungsgegenstand ist die integrierte Lieferkette, in der z.B. die gesamte Kundeninteraktion, vom Auftragseingang bis zum Zahlungseingang, alle Materialbewegungen und Transformationen sowie jegliche Marktinteraktion vom Rohstofflieferanten bis zur Produktauslieferung an den Endkunden enthalten sind. Für die unterschiedlichen Formen von Supply Chains werden Handhabungsempfehlungen, Schnittstellenkonfigurationen, EDV-Protokolle, Vertragsvorschläge, Kennzahlensysteme zur Steuerung usw. zur Verfügung gestellt.
Auf der höchsten Ebene "top level" sieht das Modell für jede Wertschöpfungsstufe, d.h. für jeden einzelnen Betrieb, fünf Basis-Prozesse vor: Planung (Plan), Beschaffung (Source), Leistungserstellung (Make), Lieferung (Deliver) sowie Retouren (Return). Gleichzeitig sind damit die Schnittstellen zwischen den Wertschöpfungsstufen definiert. Über die Konfigurations- und die Gestaltungsebene wird das Modell immer konkreter, so dass für die Implementierungsebene Empfehlungen gegeben werden, wie eine individuelle, die Unternehmensspezifika berücksichtigende Umsetzung in Eigenverantwortung zu realisieren ist.
Das SCOR-Modell soll also Supply Chain Managern helfen, die schwierige Aufgabe der Gestaltung und des Betriebs einer Supply Chain zu bewerkstelligen. Ist ein Glied in der Lieferkette dominierend, werden Manager dieses Unternehmens in der Regel so genannte "Supply Chain Leader" oder Vorsitzende eines gemeinsamen "Supply Chain Committees" sein.
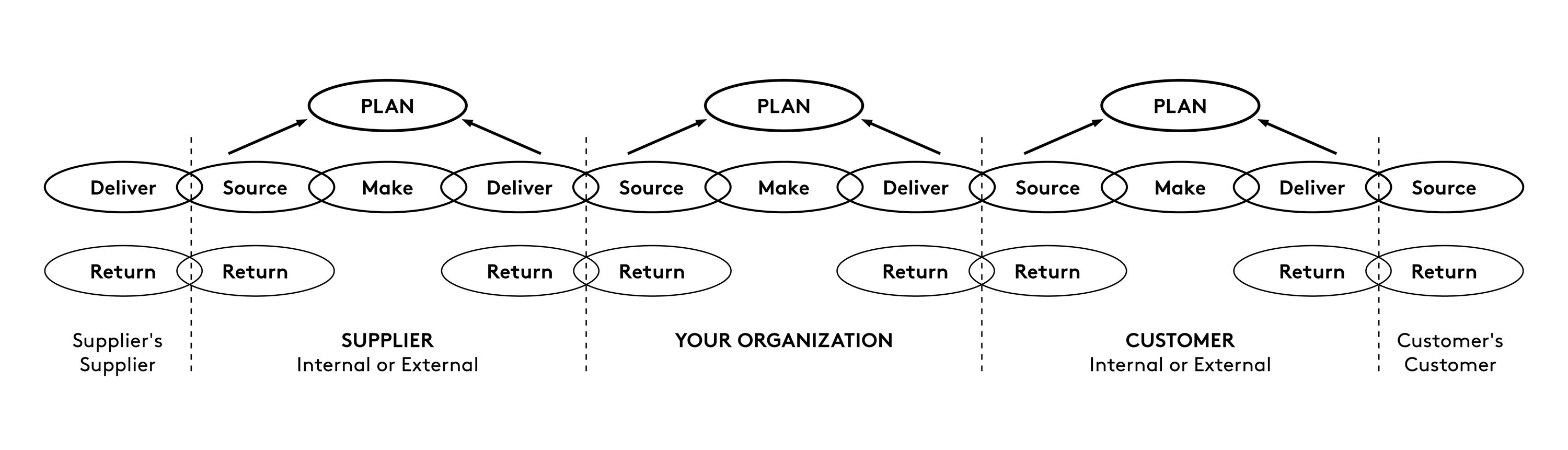
Warum ist die enge Abstimmung erforderlich?
Durch die Verteilung von Wertschöpfungsstufen auf mehrere unabhängige Unternehmen besteht die Gefahr, dass die einzelnen Glieder der Lieferkette proprietäre Optimierungen vornehmen, sich also nicht untereinander abstimmen. Insbesondere, wenn der Handel Element der Lieferkette ist, ergeben sich große Risiken, welche unter dem Phänomen des "Peitscheneffekts" (englisch "bullwhip effect") bekannt sind.
Angenommen, ein Einzelhändler stellt fest, dass er in der vergangenen Periode die Nachfrage nach einem Gut nicht voll bedienen konnte. Zudem nimmt er an, dass in seinem Einzugsgebiet die Nachfrage nach dem Produkt weiter steigen wird. Als Konsequenz wird er nun eine größere Menge bestellen und sein Lager füllen (so genanntes "forward buying"). Der Großhändler liefert die Ware und erkennt, dass hier ein größerer Bedarf entstanden ist. Um sicher zu sein, dass er auf weiter steigende Bestellungen zeitnah reagieren kann, bestellt er eine entsprechend größere Menge bei dem Hersteller. Dieser reagiert seinerseits mit der Planung der Fertigung zusätzlicher Lose, woraufhin beim Zulieferer entsprechende Mengen geordert werden.
Diese Reaktionen in der Lieferkette entstehen jeweils mit einem Zeitverzug. Die bestellten Mengen erhöhen sich von Stufe zu Stufe um Sicherheitsmengen. Insgesamt schaukelt sich das Mengensystem stromaufwärts auf. Sollte die erwartete Nachfrage der Konsumenten nicht eintreten, ist die Lieferkette mit Aufträgen versehen, welche nicht zum Verkauf führen.
Der Peitscheneffekt konnte bereits in verschiedenen Branchen festgestellt werden, z.B. in der Konsumgüter (Procter & Gamble, Campbell Soup), Elektronik (Hewlett-Packard, IBM, Motorola), Automobil (Generla Motors), Pharma (Eli Lilly). Eine eng koordinierte Supply Chain unter Einsatz aufeinander abgestimmter IT-Systeme kann diesen beschriebenen Effekt verhindern.
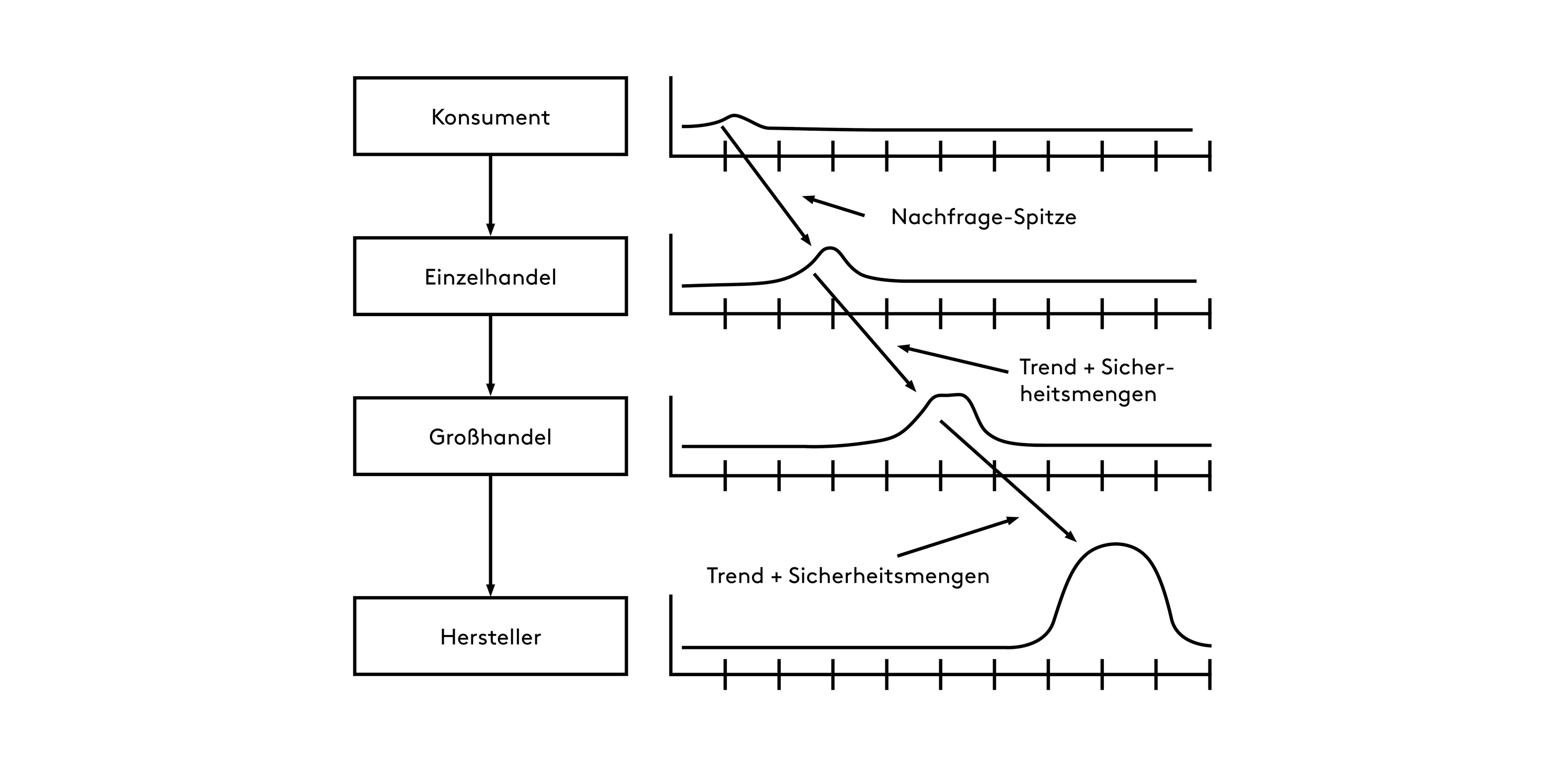
Welche Effekte erzielt ein Supply Chain Management?
Dem Supply Chain Management werden erhebliche Verbesserungspotenziale zugeschrieben. So hat IBM innerhalb eines Geschäftsjahres Kosteneinsparungen in Höhe von sieben Milliarden US-Dollar, Wal Mart in Höhe von 25 Prozent realisiert. Die Beratungsgesellschaft PRTM/pwc will folgende möglichen Effekte über die gesamte Lieferkette festgestellt haben (alle Zahlen aus Werner, 2013, S. 1):
- Lagerbestände: Reduktion um 50 bis 80 Prozent
- Liefertreue: Erhöhung um 10 bis 25 Prozent
- Überfällige Bestellungen: Rückgang um 70 bis 90 Prozent
- Auftragsabwicklungszeit: Reduktion um 40 bis 75 Prozent
- Gemeinkosten: Senkung um 10 bis 30 Prozent
- Herstellzyklen: Verkürzung um 30 bis 90 Prozent
In ihrer empirischen Untersuchung identifizierten Bolstorff et al. (2007) sechs Möglichkeiten zur Umsatz- bzw. Gewinnsteigerung durch ein SCOR-basiertes Supply Chain Management: Verringerung entgangener Aufträge, Reduktion der Durchlaufzeit der Auftragsabwicklung, ständige Verfügbarkeit der Lagerbestandszahlen in Echtzeit, Vermeidung nachträglicher Änderungen von Bestellaufträgen, Reduktion inaktiver Lagerbestände, Reduktion der Prozesskosten in der Beschaffung (Verschwendung). Insgesamt ermittelten die Autoren ein Umsatzwachstumspotenzial von drei Prozent.
Wenngleich nicht immer eindeutig und allein dem Supply Chain Management diese Erfolge zugeschrieben werden können, so bringt die bewusste Gestaltung der Lieferkette zusammengefasst doch erhebliche Möglichkeiten.